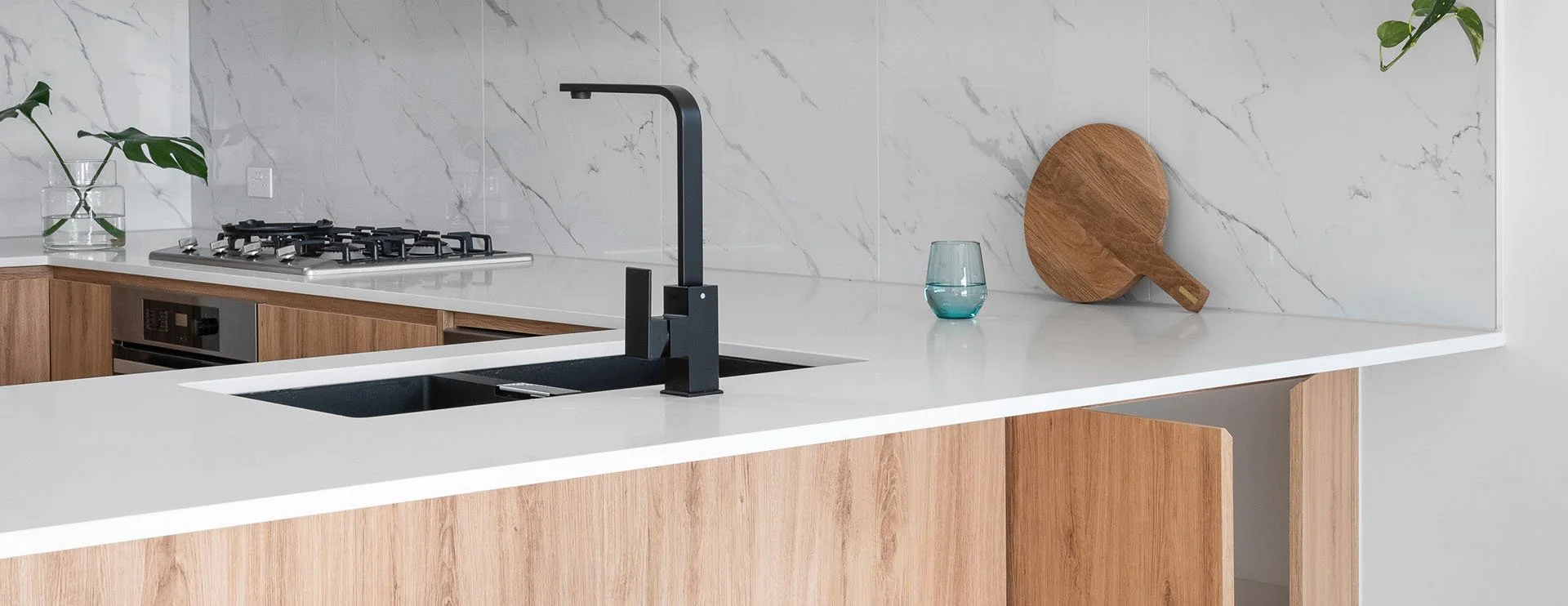
Case Study — Allens Kitchens, Gold Coast
Allens Kitchens & Bathrooms increase production volume and efficiency with Cabinet Vision
“I’m able to use my time more wisely in the business rather than doing some more generic things, such as running the saw, and it’s been able to give me a bit more free time outside of work, too,”
—
Rene Hartlief
Production Manager at Allens Kitchens & Bathrooms, Gold Coast
Initial Engagement.
Tackling a modern workload with the tools of yesteryear is a daunting task, which is why Allens Kitchens & Bathrooms increased production volume and reduced error by making the switch to CNC.
Founded on the Gold Coast of Queensland by owner Don Allen, Allens Kitchens & Bathrooms specializes in residential projects and prides itself on never telling clients that “it can’t be done.” The family business, which opened its doors more than two decades ago, has since built a solid reputation on professionalism, dedicated service, and the quality of its custom products.
“They started off doing everything the old-school way, and it’s grown ever since,” says Production Manager Rene Hartlief, who has been with Allens Kitchens & Bathrooms for over two years. Hartlief, who owned a woodworking company prior to joining Allens, encouraged Don Allen to implement CNC machinery and the software needed to drive it.
“I’d known for years the benefits and the quality of the work that would come out of it,” Hartlief says. “We did talk to other business owners that had made that change, and they all said that it was a wise decision.”
Understanding the needs.
Allens Kitchens & Bathrooms purchased the Cabinet Vision design-to-manufacturing solution from Planit Cutting Edge Solutions in 2016, and learned how to utilize the system before going forward with the purchase of a CNC router.
“Having the software before having CNC installed was beneficial because we were familiar with the program, and we understood the basics,” Hartlief says. “Once we purchased the CNC, you could really see the potential of the program and things you could do with it.”
Prior to the integration of CNC machinery, the shop utilised Cabinet Vision’s design and project organisation tools to reduce error and streamline the production process.
Projects in Cabinet Vision typically begin when the dimensions of the space in which the job will be built are entered into the system. From there, realistic graphics and easy-to-use design tools allow users to create detailed drawings of finished projects within that virtual space. Users are then able to generate cutsheets and assembly sheets to provide error-free instructions as parts move through the shop.
“It enabled us to produce more accurate shop drawings, both here in the shop and for the customer. It was also a benefit for doing cutsheets.”
Clear Achievements
After the company installed a CNC router to pair with Cabinet Vision, it was able to use its detailed drawings as a basis for toolpath application. Once drawings are complete, Hartlief can generate toolpath with the click of a button and send CNC code to the shop floor.
“It’s been a very seamless transition, so Planit’s been very easy to deal with. Even with tech support, the times that I’ve called up about that, the guys there are very knowledgeable, and they’re able to help us out and fix any problems we’ve had,” Hartlief says. “I’d recommend Planit to any cabinet shop. I’ve looked at other programs over the years, too, and definitely Planit is the way to go because it’s simple, it does everything you need it to, and the service is there, too.”
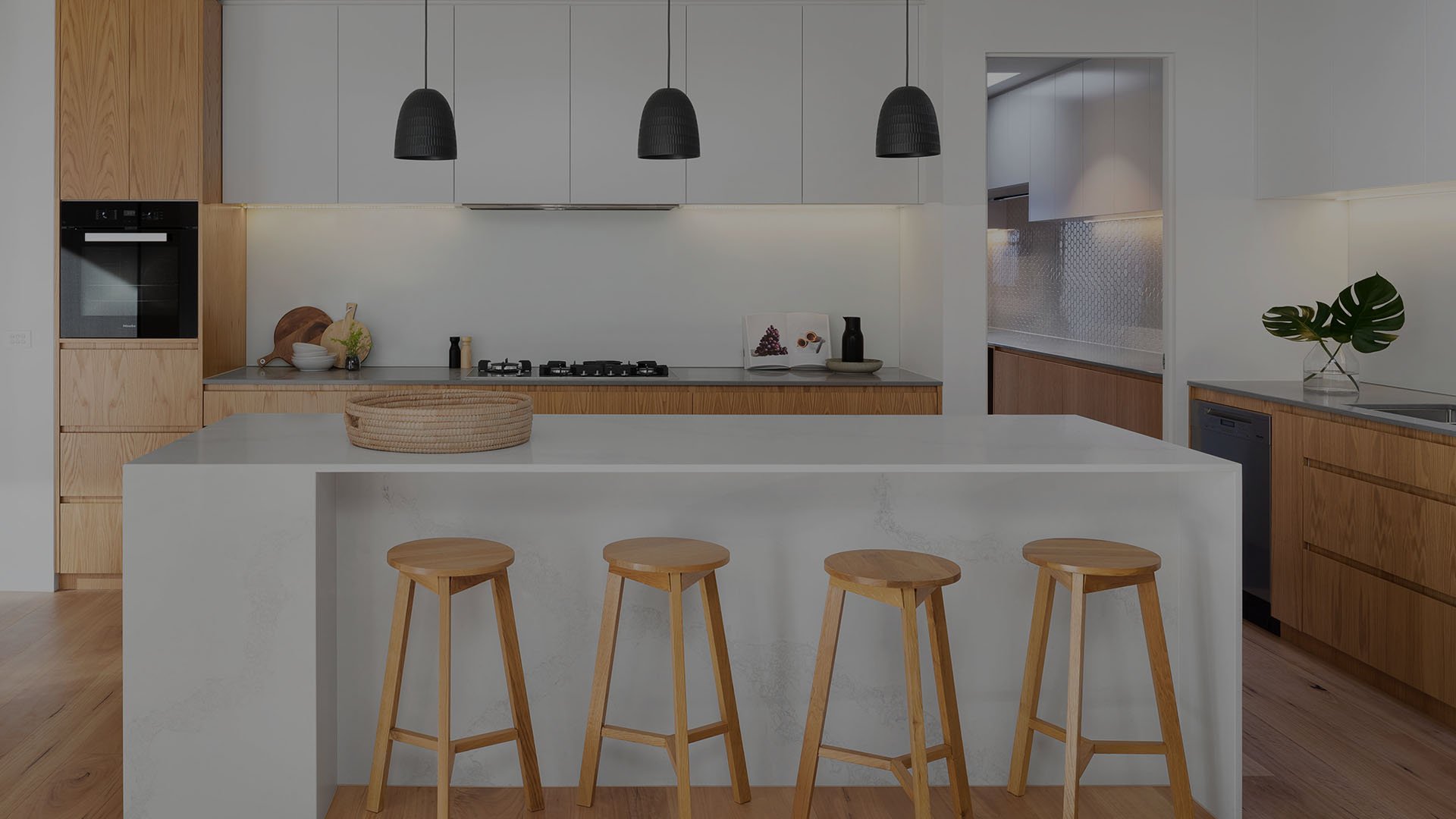
Work with us.